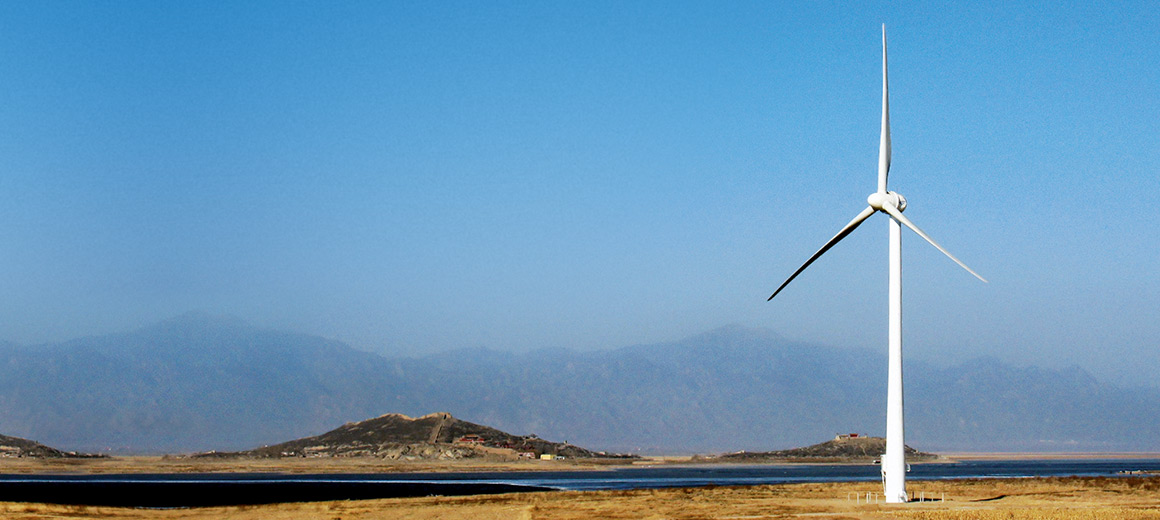
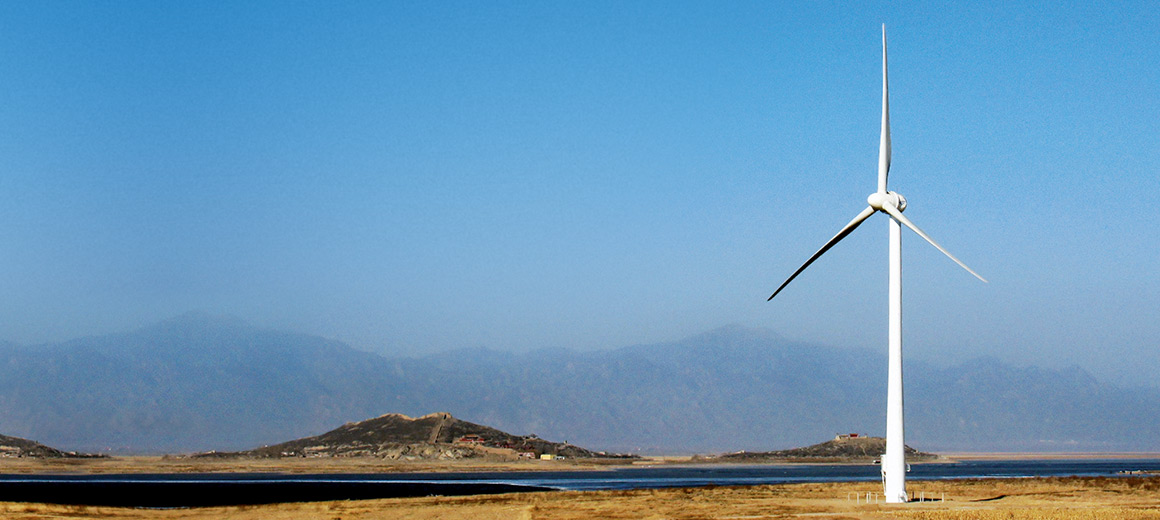
An Embedded PC installed in the tower base acquires and processes all data, monitors the grid feed-in and communicates with the central control room. Safety and measurement technology as well as condition monitoring are seamlessly integrated into the controller via appropriate I/O modules. The converter in the base of the tower, the I/O system for operational management in the nacelle and the pitch controller in the hub are connected to the master controller via EtherCAT. Lower-level fieldbuses such as CANopen, PROFIBUS, and Ethernet TCP/IP can be relocated to the field via fieldbus master or slave terminals for the control of subsystems. The universal use of EtherCAT accelerates communication, and at the same time simplifies the project planning, programming and cabling of the wind turbine. Open hardware and software interfaces enable integrated communication from sensors to cloud systems.
For operational management in tower base and nacelle, a complete hardware and software solution programmed with TwinCAT 3 in IEC 61131, C/C++ and/or MATLAB®/Simulink® is available. Interfacing with higher-level control systems is based on internationally standardised telecontrol protocols. Servers that allow remote access to the control system are integrated into the Embedded PC. TwinSAFE enables the integration of the conventionally hard-wired, higher-level safety chain into the automation system. Communication between tower base and nacelle is implemented inexpensively and flexibly over fibre-optic cables using EtherCAT. Beckhoff offers a complete control solution for pitch systems. The DIN rail-mountable Beckhoff Embedded PCs with line-connected EtherCAT I/O Terminals or IP67-rated Box modules are ideally suited to the collective or individual adjustment of the rotor blades. Encoder terminals for all types of blade pitch sensors are available as standard.