In the midst of the mobility revolution and the subsequent expansion of electric vehicle production facilities, Beckhoff technology has been steadily finding its place in battery manufacturing and electric motor production for several years. Thanks to our many years of experience in body construction, tire production, and process, assembly, and handling technology, our customers can always rely on our in-depth technical expertise. As a close partner of automotive OEMs and machine builders, we also actively promote the standardization of machine communication in working groups such as the VDMA Battery Production group. A large number of references from a wide range of sectors across the automotive industry confirm the effectiveness of our control solution.
Current applications
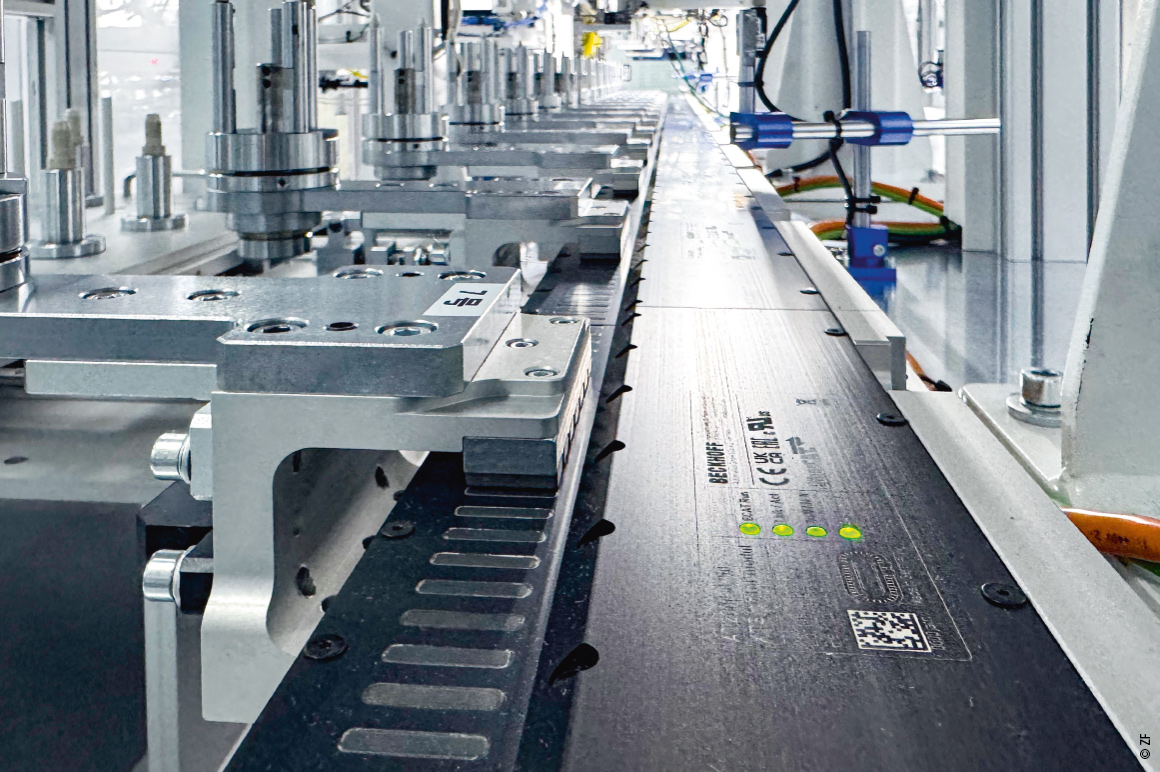
PC-based control and EtherCAT for a new era of chassis-by-wire technology
As a global leader in automotive components, ZF is at the forefront of the mobility transformation with its innovative and sustainable technology. A pioneer in chassis-by-wire systems, ZF also requires advanced manufacturing technology for its brake-by-wire products to achieve faster, more efficient production at a higher level of quality. The production line in China comprises numerous assembly lines with complex core processes. A comprehensive range of Beckhoff components and solutions were used to overcome the associated challenges.
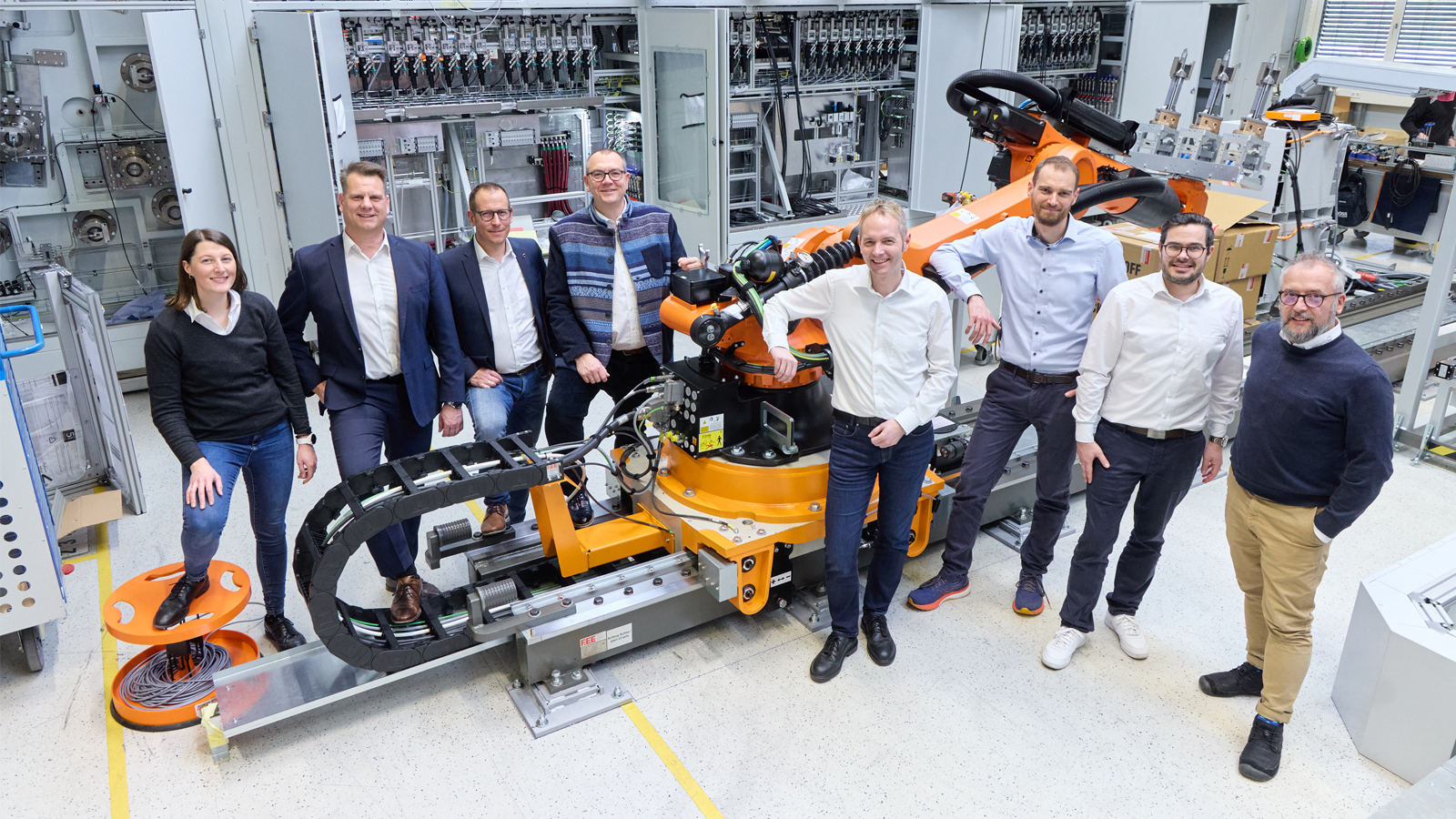
PC-based control for trickle impregnation systems for electric motor production
Potting the windings is crucial for the performance and durability of electric motors. This is why many car manufacturers rely on impregnation systems from bdtronic. The process solution provider from Weikersheim combines its comprehensive process expertise in dispensing, plasma, impregnation, and heat staking technology to create individual, cycle time-optimized systems with the help of PC-based control.
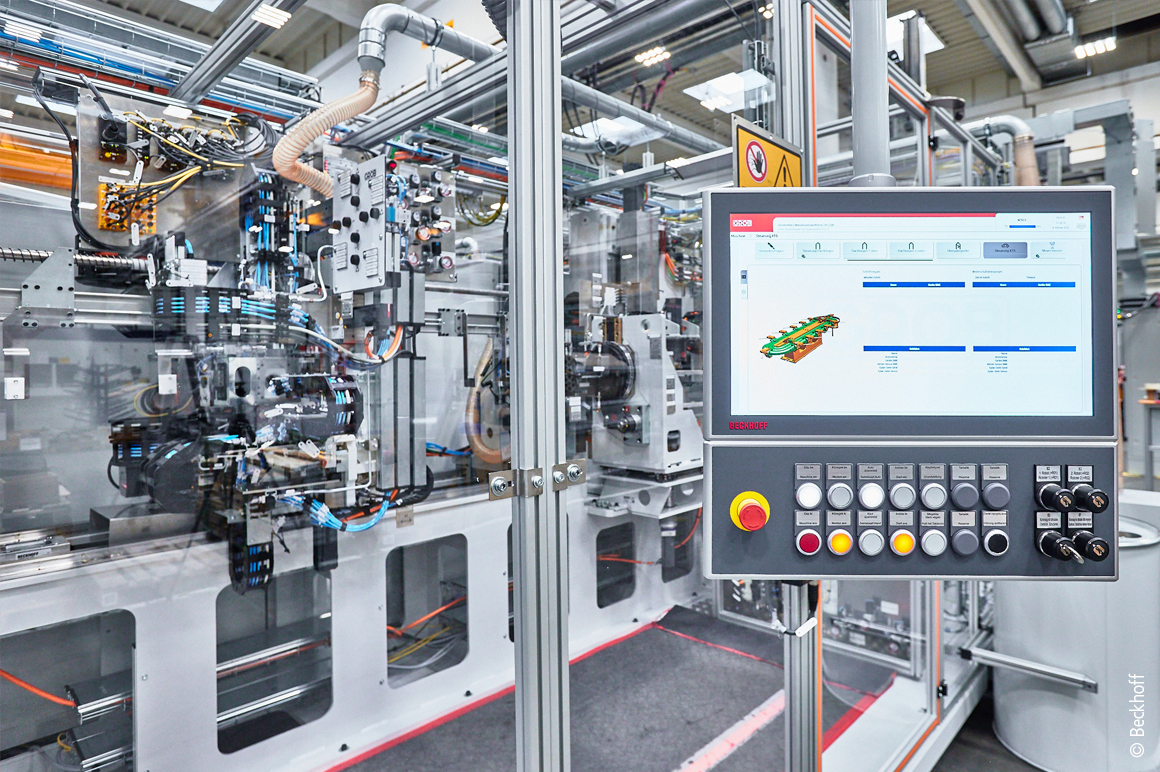
Flexible control technology increases efficiency in hairpin stator production lines
GROB, a machine tool manufacturer, is actively addressing the rapidly increasing significance of electromobility by implementing high-volume production and assembly systems. The decisive factors here are very short cycle times and equally fast process sequences, enabled by PC- and EtherCAT-based control and drive technology from Beckhoff. A sophisticated production machine for hairpins, which the stator winding rims of electric motors are formed from, illustrates the advantages of this optimally scalable automation solution – for example, with TwinCAT 3 on a C603x ultra-compact Industrial PC as the central control and with the XTS transport system.
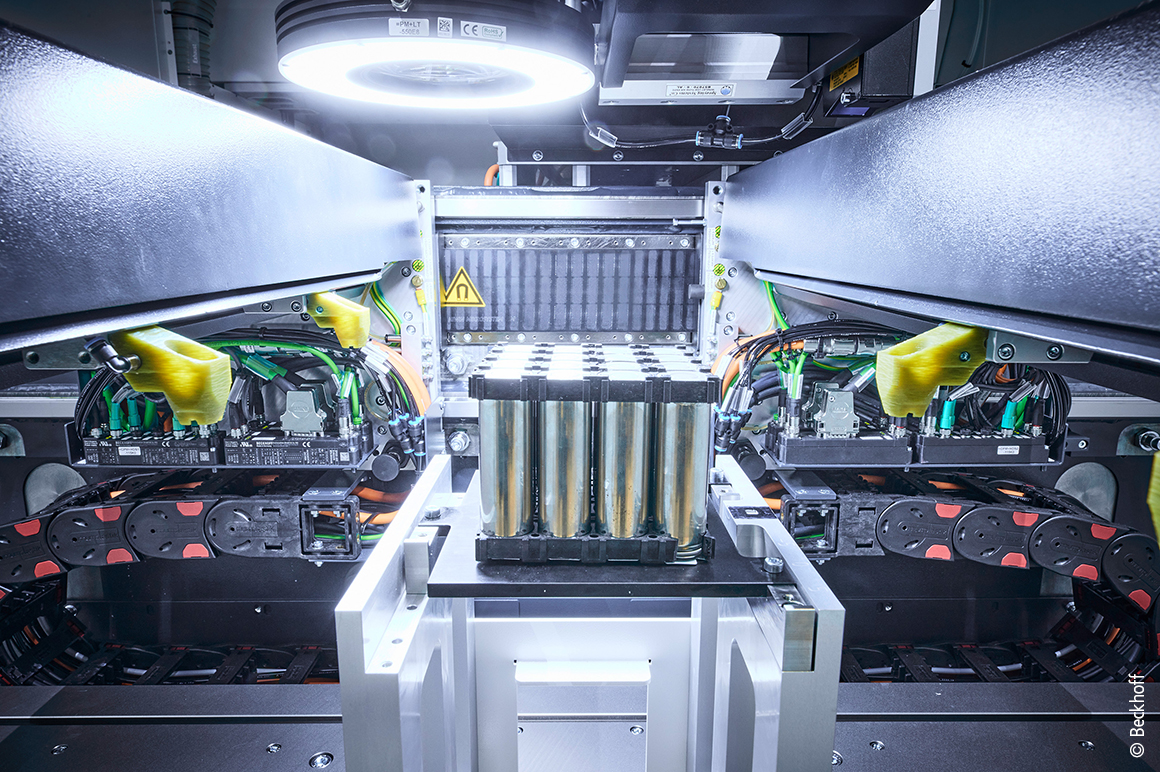
Automation for highly precise and efficient production of lithium-ion battery modules
The rapidly growing electromobility market calls for particularly efficient manufacturing processes when it comes to the production of lithium-ion battery systems. This is where the BLS 500 laser welding system from Manz makes for an ideal solution, as it allows individual battery cells to be precisely contacted and connected to form battery modules. A high level of efficiency is ensured by means of a graphical programming tool and a virtual commissioning tool from Manz, as well as rapid PC-based control technology from Beckhoff and the continuous OPC UA communication this facilitates.
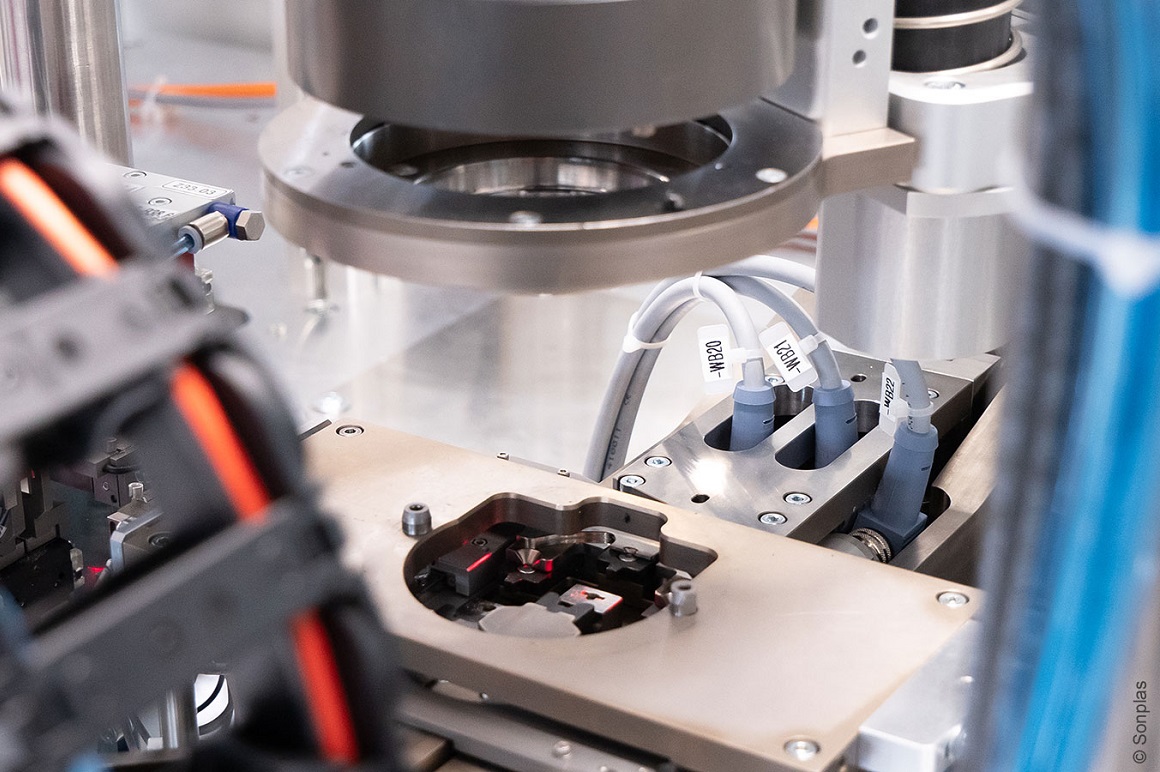
TwinCAT achieves high clock rates in the pre-assembly of stators
As new trends in mobility continue to emerge, Sonplas, a special machine manufacturer, is one of many companies that has been sharpening its focus on projects from the field of e-mobility in recent years. The company’s areas of activity include developing machines for rotor and stator assembly of electric motors. When it comes to the pre-assembly of stators, Sonplas relies on PC-based control from Beckhoff and benefits from the short cycle times of TwinCAT for maximum output and efficiency.