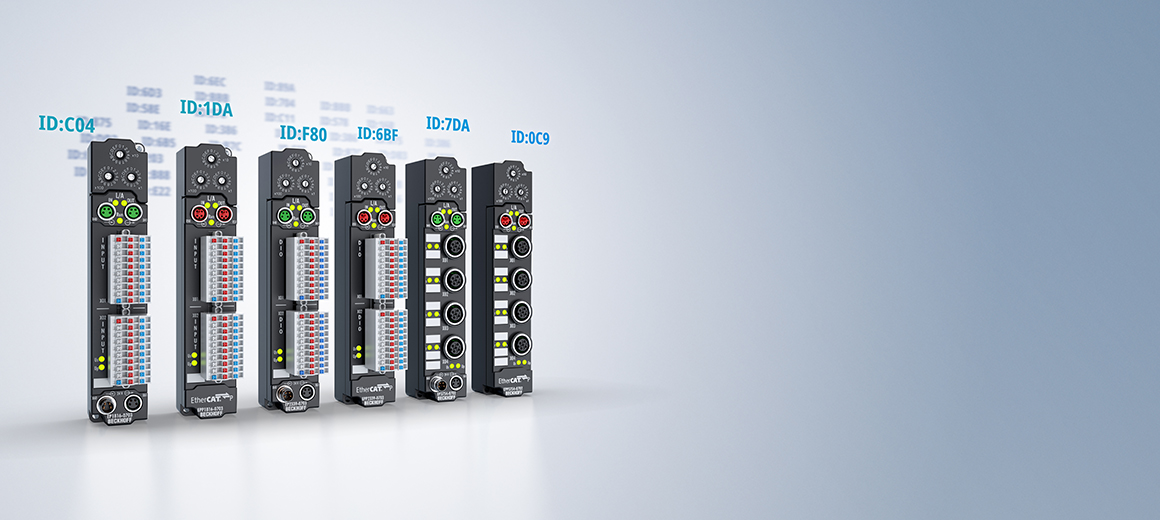
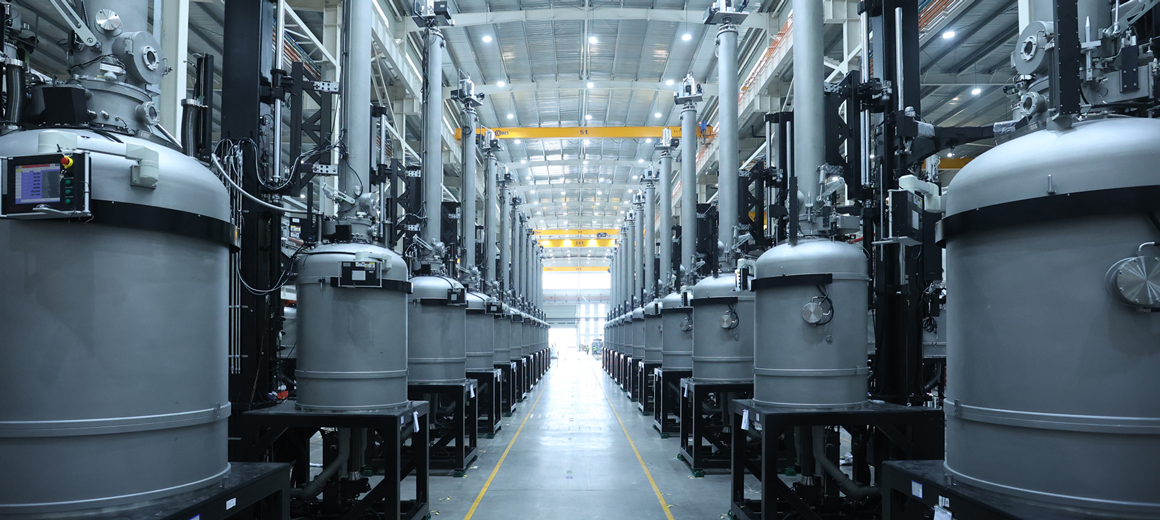
Semiconductor production for photovoltaic equipment
Flexible automation of single-crystal furnaces increases competitiveness
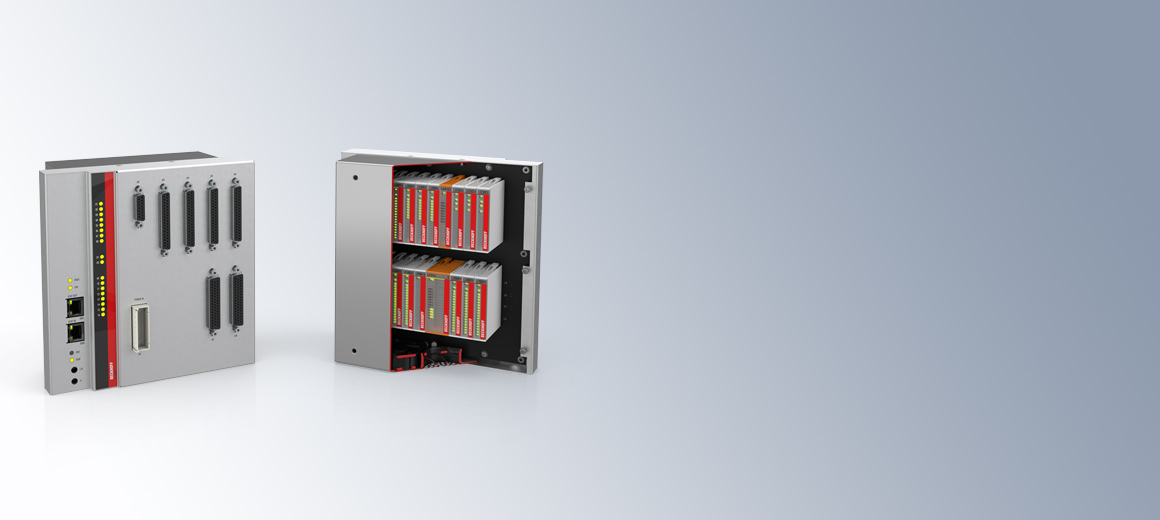
EtherCAT plug-in modules for the semiconductor industry
from standard EtherCAT I/Os to safety I/Os
Headquarters India
Beckhoff Automation Pvt. Ltd.
+91-20-6706 4800
info@beckhoff.co.in
www.beckhoff.com/hi-in/
Flexible automation of single-crystal furnaces increases competitiveness
from standard EtherCAT I/Os to safety I/Os
From automation and electromobility to communications and AI, many high-growth technologies owe their performance to high-tech chips from the semiconductor industry. Future demand will significantly exceed manufacturers’ production capacities. To close the gap, existing semiconductor plants must undergo further automation and new, highly efficient fabs must be built worldwide. A key technology in this area is EtherCAT, the Industrial Ethernet technology from Beckhoff Automation.
Do you have any questions?
EtherCAT is an Industrial Ethernet technology developed by Beckhoff in 2003 that is now considered the global standard in the semiconductor industry. There are three reasons for this: EtherCAT is ultra-fast, optimized for real-time communication, and a technology standard that we have made open and available to everyone.
Thousands of manufacturers from various industries – including numerous players from the semiconductor industry – are involved in the maintenance and further development of this standard as part of the EtherCAT Technology Group, which was founded in 2003. This ensures transparency and tailor-made solutions. EtherCAT was declared a SEMITM standard in 2007. The next milestone was the establishment of a separate Semiconductor Technical Working Group (TWG) within the ETG in 2011. This ensures that the industry always receives up-to-date EtherCAT solutions that are optimized for its requirements.
As the inventor, Beckhoff is by far the largest and most experienced provider of EtherCAT-based control and automation solutions. Both third-party EtherCAT devices and systems that work with other protocols can be integrated into these solutions. This applies without restriction and guarantees maximum design freedom.
The origins of the EtherCAT product range lie in the real-time processing of I/O signals. Today, Beckhoff offers a product range that is unparalleled in scope. It covers all of the requirements of the semiconductor industry. The range includes fieldbus-independent I/O modules in all performance and protection classes as well as EtherCAT master terminals and box modules.
However, conventional analog and digital I/O applications form only the foundation of the Beckhoff EtherCAT environment. An entire world of modular automation solutions has been created that builds on this, covering all the functionalities of modern control environments. EtherCAT-based communication modules are also available, for example for power measurements, for evaluating various encoder interfaces, or for controlling a wide range of motors and drive systems. In short, through the combination of standard signals with special functionalities, Beckhoff has the right solution for every automation task.
Effective safety solutions for hardware and software are a must in the semiconductor industry. They can be implemented in an automated and efficient way exclusively with Beckhoff. This is ensured by our TwinSAFE technology in conjunction with the international Safety over EtherCAT standard, which enables real-time transmission of safety-relevant data via the installed EtherCAT network.
The advantage of this is that there is no need to set up a separate safety network. Instead, all safety functions and applications are executed directly via the connected TwinSAFE Logic-capable components and modules. The range of Beckhoff solutions is vast and includes analog and digital I/O components as well as solutions for all other functionalities required in the semiconductor industry, such as modules for drive systems and measurement technology