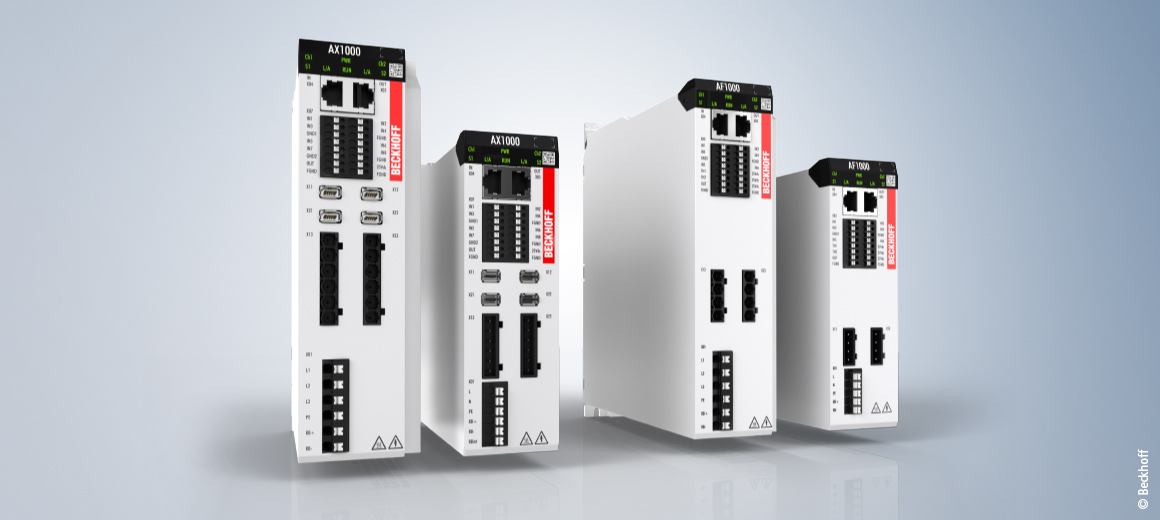
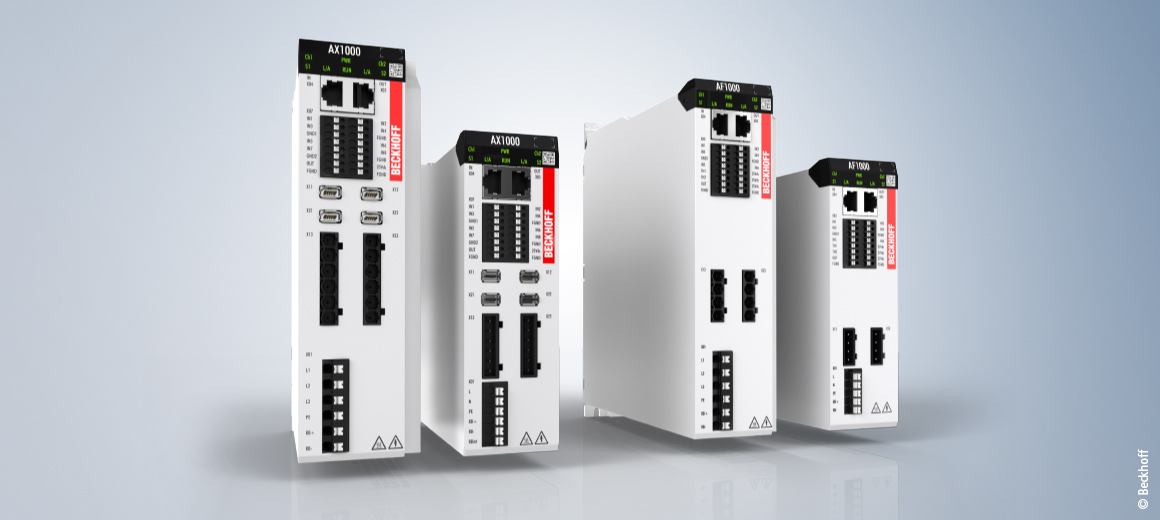
New economy drive system designed for cost-sensitive applications
Beckhoff has developed two new drive series on a shared platform, incorporating a host of innovative ideas: the AX1000 economy servo drives and the AF1000 economy variable frequency drive. These new additions complement the existing portfolio perfectly, particularly by expanding coverage for cost-sensitive applications. To that end, the development focused heavily on ensuring high cost efficiency and minimizing complexity.
Before the start of development, intensive discussions were held with customers to define their needs and the most important product features of a new drive. These insights provided a solid foundation for clear design specifications. The aim of this new device generation was to deliver core servo functionality without adding features for niche applications. This strategy made it possible to create extremely cost-effective, streamlined devices with fewer components, resulting in significantly faster assembly times and more efficient production processes. Additional benefits for users include the excellent serviceability and fast, simple, and intuitive commissioning.
Development of the AX1000 series included both single-phase, compact devices and three-phase servo drives running in parallel. Building on this foundation, Beckhoff quickly launched another device series in the form of the AF1000 variable frequency drives. The AX1000 platform is also ideally suited for the development of a series of variable frequency drives – a new product range for Beckhoff targeting a market segment under even greater price pressure. As with previous Beckhoff series, the AX1000 servo drives are available in both single-axis and dual-axis versions, which is by no means standard for variable frequency drives. Beckhoff always incorporates new and innovative features when developing a product. In this case, a dual-axis version of the variable frequency drives was introduced. To our knowledge, this is a worldwide first and enables a significantly higher maximum packing density in the control cabinet. The dual-axis device also delivers substantial cost savings by allowing key components to be used for two variable frequency drives.
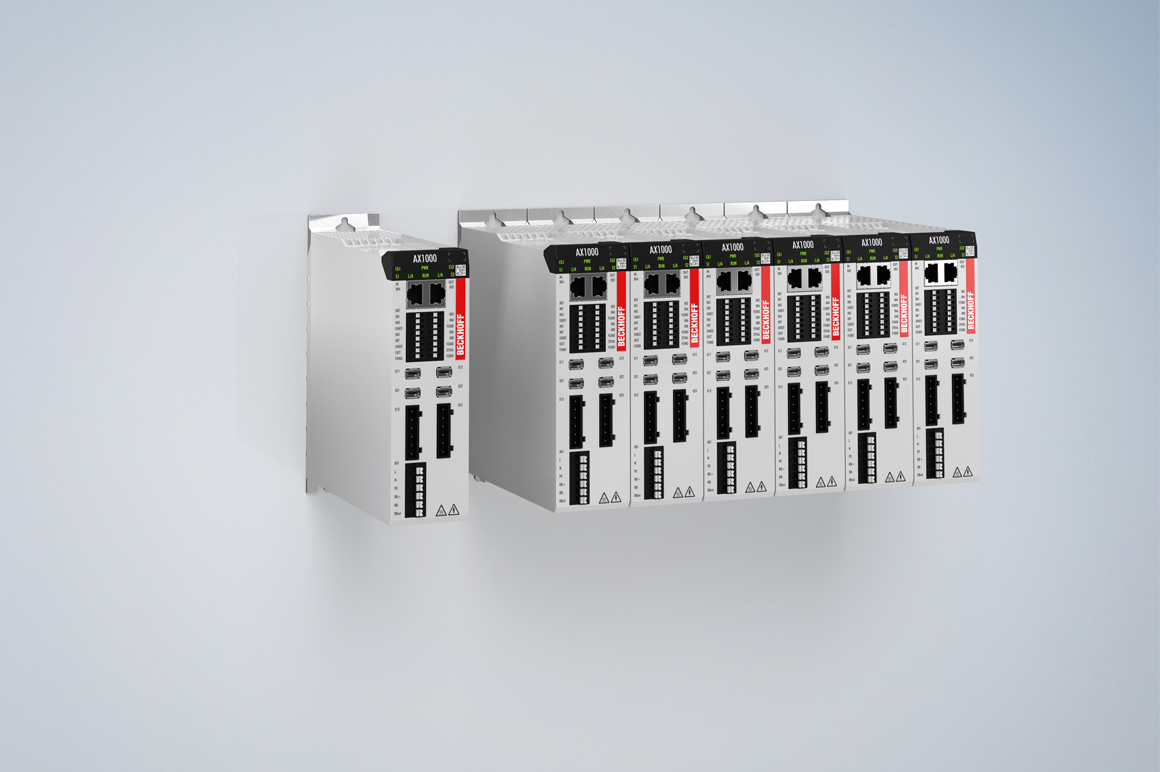
AX1000: optimized, efficient servo drive for low power requirements
The AX1000 servo drive is available with a rated current range of 1.65 to 6.9 A and is fully integrated into TwinCAT. It is available in two different connection versions: for lower power ratings up to 2.2 kW with single-phase 1 x 230 V AC input, and for higher power ratings from 1.1 kW to 4.5 kW with three-phase 3 x 400 V AC input. Despite its compact dimensions, it features an integrated power supply, DC link capacitors, and a ballast circuit.
The cost-optimized plastic housing of the AX1000 is immediately noticeable. Its intelligent PCB design eliminates the need for a stainless steel housing to reduce electromagnetic emissions. Despite being designed for maximum efficiency and compactness, the devices can be mounted side by side in the control cabinet without spacing. With the exception of optional safety inputs, all connections are accessible from the front, which not only makes wiring the devices easier but also improves control cabinet organization.
The AX1000 eliminates the need for an external 24 V DC power supply, as the drive generates the control voltage for I/Os and the holding brake supply directly from the DC link. This saves considerable space and provides the added benefit of the 24 V DC generation continuously lowering the DC link voltage, providing a greater energy reserve for dynamic braking operations. The AX1000 is also equipped with a very high-capacity design to efficiently store as much energy as possible for braking processes without having to activate the internal braking resistor. This reduces additional heat generation in the control cabinet. For applications with extremely high kinetic energy, an external braking resistor can be connected to each device.
Compliance with EMC directives requires an external mains filter, which, together with the device’s integrated interference suppression, ensures that EMC limits are not exceeded. A key advantage is that a single filter can be used for collective interference suppression of multiple devices, and suitable filters are available for different current ratings. With their very low leakage current, the devices are easier to use with residual current circuit breakers. The AX1000 servo drives also support Beckhoff’s established One Cable Technology (OCT). Partially shielded motor cables for the AX1000 further reduce sheath diameters and bending radii while lowering costs for components such as drag chains, cable channels, and fixings.
The AX1000 supports various motor types, including AM8000 synchronous servomotors with OCT, asynchronous motors, and reluctance motors, each with or without feedback. In applications where maximum dynamics are not required, reluctance motors offer an efficient and cost-effective solution. Setting up the AX1000 to operate these motors requires minimal effort. For dual-axis devices, two different motor types can be selected independently for each axis.
The AX1000 is equipped with the TwinSAFE STO/SS1 function as standard. Parameterization is carried out via FSoE, with activation possible via either FSoE or the optional safety I/Os. A key advantage is the clocked implementation of the safety I/Os, which eliminates the need to exclude wiring faults, allowing for direct connection of an emergency stop switch. Additional safety functions are available with the TwinSAFE Safe Motion option.
The AX1000 is integrated into the TwinCAT system via EtherCAT, providing full convenience for commissioning, operation, and diagnostics. All tools available for the larger AX5000 and AX8000 drives, such as TwinCAT 3 Drive Manager 2, TwinCAT 3 Autotuning, TwinCAT 3 Bode Plot, and TwinCAT 3 Cogging Compensation, can also be used with the AX1000 servo drive. Integration into the Motion Designer makes it easier to tailor the drive axes to suit individual requirements.
AF1000: universal variable frequency drive for low power requirements
Like the AX1000 servo drive, the AF1000 variable frequency drive is fully integrated into TwinCAT and is available in two different connection versions: for lower power ratings up to 2.2 kW with single-phase 1 x 230 V AC, and for higher power ratings from 1.1 kW to 4.5 kW with three-phase 3 x 400 V AC. The power ratings within the series are based on the general standard range for asynchronous motors. The dual-axis version of the AF1000 makes the device even more compact and cost-effective, as essential components such as the EtherCAT interface, microcontroller, power supply, and housing are used for both axes.
The AF1000 shares many properties with the AX1000, which was developed based on the same platform. These include the plastic housing, high DC link capacitance, internal 24 V control voltage supply, and the connection via external interference suppression filters. The AF1000 is the ideal complement to the servo drive, as it also shares the same dimensions. This allows for easy expansion of an AX1000 system with the AF1000, particularly when certain axes in an application do not require servo control. As a result, users can benefit from significant cost savings.
The AF1000 uses an unshielded motor cable and supports the connection of motor temperature sensors such as PT1000, KTY, or LPTC600, with evaluation performed directly within the device. Although holding brakes are rarely used with asynchronous motors, some motors equipped with brakes may require higher voltages. As a result, the device does not include a direct holding brake connection. If required, a digital output is available for controlling an external relay.
The AF1000 supports asynchronous motors, reluctance motors, and servomotors with sensorless operation – i.e., without position encoders – via U/f characteristic curve or vector control. This variant can be used to create a cost-effective drive system for simple applications such as belt drives, pumps, and fans. For dual-axis devices, two different motor modules can be selected independently for each axis.
The AF1000 is available with optional TwinSAFE STO/SS1 safety functions, with or without I/Os. Parameterization is carried out via FSoE, as with the servo drives, and activation is possible via either FSoE or the optional safety I/Os. The I/Os provided with the safety option feature the same clocked implementation as that described for the AX1000.
The AF1000 is seamlessly integrated into the TwinCAT system via EtherCAT, providing full convenience for design, commissioning, operation, and diagnostics. Just like the other Beckhoff servo drives, the AF1000 variable frequency drive is also commissioned using TwinCAT 3 Drive Manager 2, meaning users do not need to familiarize themselves with a separate dedicated tool.