Plastic Framework increases flexibility and dynamics for more efficient processes
The economical use of all resources is important in plastics processing. BBM, a machine builder specializing in blow molding machines based in Langenberg, Germany, therefore attaches great importance to all-electric machines and innovative process control with the TwinCAT 3 Plastic Framework. Automated with PC-based control from Beckhoff, energy consumption is reduced by producing higher quantities combined with an efficient use of materials.
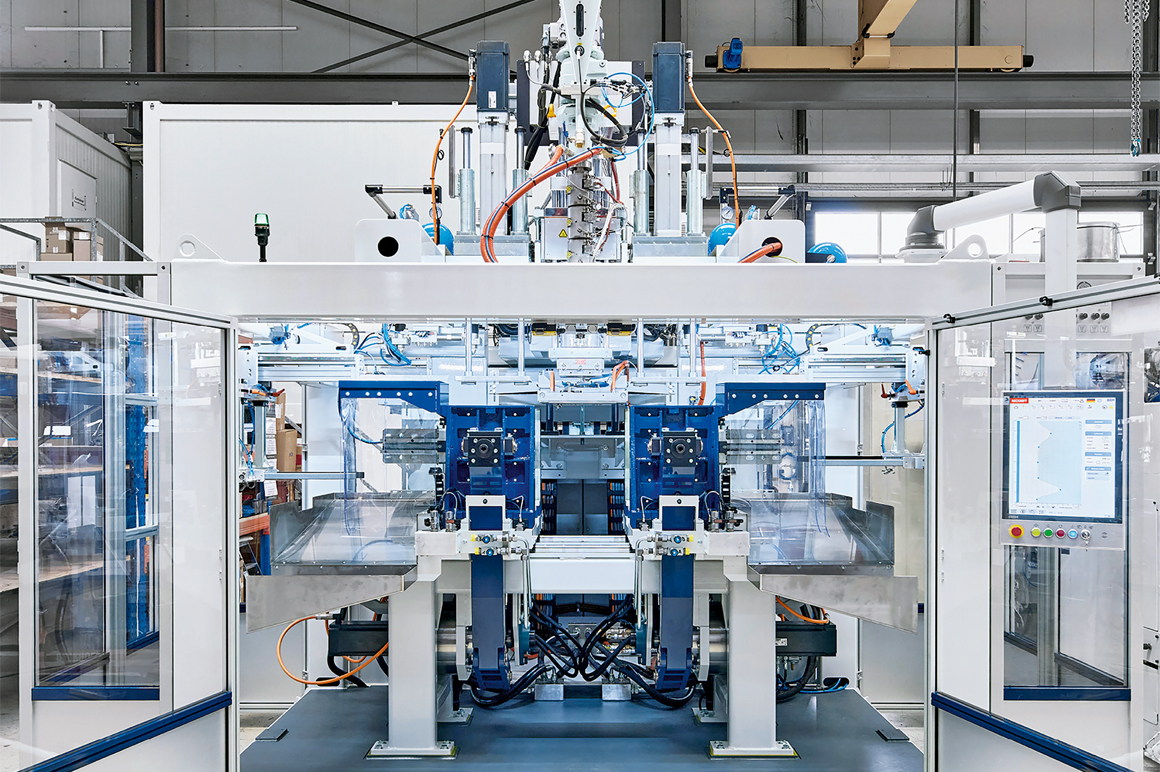
Founded as Berlin Blasform Maschinen in 1998, BBM has been developing and producing its blow molding machines in Langenberg/East Westphalia since 2003. “Around 120 employees develop and produce high-performance systems on 6,000 m²,” explains Felix Schulte, who is the second generation of the family to head the company as technical managing director. Since 2006, the company’s focus has been on all-electric machines and continuous further development of existing technologies with partners such as Beckhoff. “At BBM, systems engineering from Beckhoff acts as an extended workbench, creating the application software based on the TwinCAT 3 Plastic Framework for example, as well as configuring and assembling the system-specific control cabinets, and commissioning the systems at BBM,” says David Derksen, head of the custom machines group in systems engineering at Beckhoff, thereby highlighting the deep and trusting cooperation.
“Felix Schulte and his team always provide us with valuable impulses and ideas that are incorporated into the TwinCAT 3 Plastic Framework,” emphasizes Christian Gummich, plastics processing and hydraulics application industry manager at Beckhoff. The Plastic Framework brings together the many years of Beckhoff expertise in plastics processing, seamlessly integrating important industry-specific control functions in TwinCAT. “We therefore offer both software packages and application solutions for PLC and HMI which act as a launchpad for developing customer-specific application solutions,” adds Christian Gummich.
Flexibility and openness
The openness and flexibility of PC-based control is very important to custom machine builder BBM: The systems often have to be adapted to the customer process or the items which are manufactured on them. “PC-based control in particular offers us the flexibility and modularity to implement what are, at times, very different requirements in the application,” explains Felix Schulte. The applications range from small eye-drop bottles or 6500-liter tanks to small systems with a footprint of just four square meters or systems that fill an entire hall. “We would not be able to cover this broad spectrum without flexible automation technology and software,” emphasizes the technical managing director.
In addition to the PC-based control system, BBM also uses I/O terminals, drives, and motors – in other words, a large part of the Beckhoff portfolio. “The EcoBlow EB5 double station was completely automated using Beckhoff products,” describes Christian Gummich. In addition to a customer-specific CP3919 multi-touch Control Panel and a CX2033 Embedded PC, all drive axes in the application are driven by AM8000 synchronous servomotors or controlled by AX5000 servo drives.
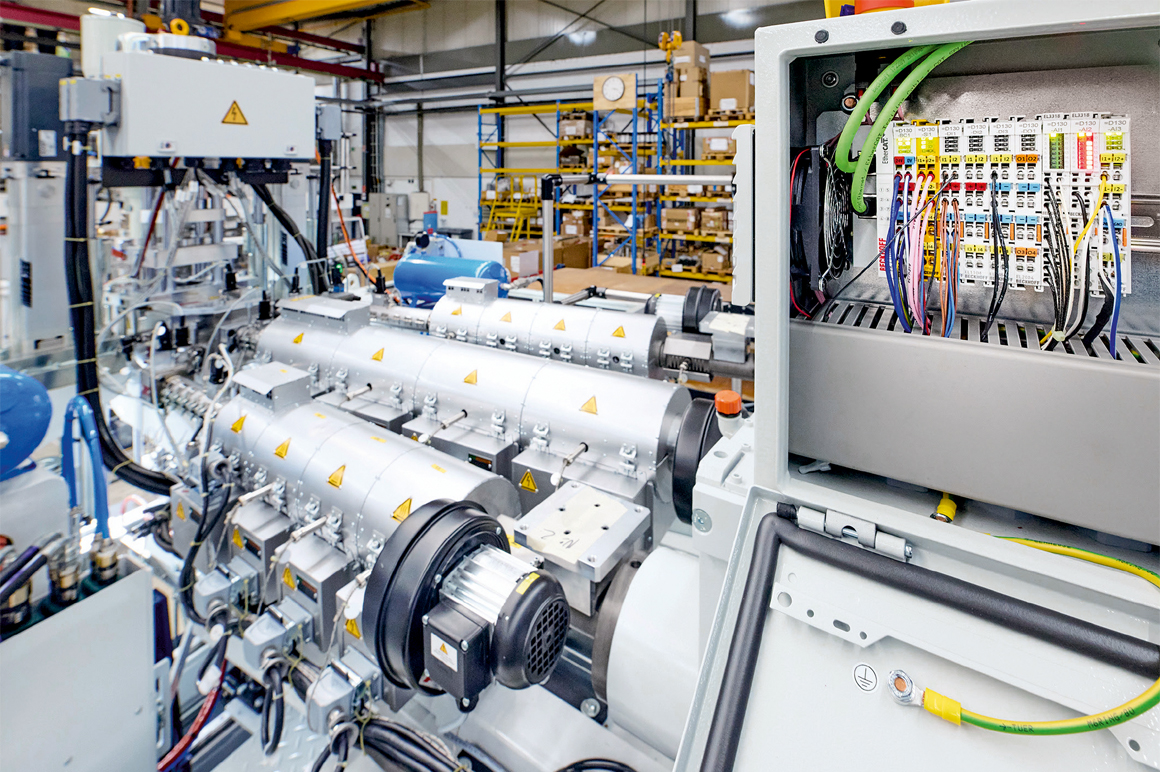
The EcoBlow EB5 has a clamping force of up to 12 t and can produce containers with a volume of up to 7 l. “This high clamping force is needed to press the plastic tightly at the seams of the mold,” says Felix Schulte. As a special feature, the machine is set up as a double station: The machine has two molding posts that move alternately under the extruder head. This provides the advantages of significantly higher machine output in relation to the footprint and a lower price compared to two individual machines. It also reduces the changeover effort and the design is very interesting for higher volume production. In addition, the machine can be equipped with up to six extruders. This is an advantage if the container wall is to contain a barrier layer, for example, or if recycled material is used.
Dynamic control for high volume production
High-performance control, short communication cycles, and dynamic drives are crucial for high throughput and high quantities to avoid downtimes in the process. “This was definitely a benefit and had a significant impact on cycle times,” says Felix Schulte. BBM’s managing director sees further potential here in the water-cooled AM8300 servomotors, which provide a significantly higher power density and greater torque for the same size.
The more dynamic the control, the more interpolation points can be used for partial wall-thickness control, for example. This reduces the consumption of material without affecting the rigidity of the canister. To improve the stability, it is important that there is more material in the corners than in the side walls. This is ensured by the partial wall-thickness control: BBM has installed two optional actuators in the area of the extrusion head. These are used to reduce the wall thickness on the surfaces and to press the material in specific areas – the corners – to provide additional stability.
Simple operation of sophisticated processes
According to Felix Schulte, the TwinCAT 3 Plastic Framework also featured an impressive user interface. Operation is straightforward using the simple visualization, which is similar to using smartphones. This is an important factor, given that end users are often struggling to find well-trained system operators. What’s more, the products are becoming increasingly sophisticated and need to be produced in large quantities using as little material as possible. “TwinCAT HMI offers a good compromise between ease of use and sophisticated setting options,” says David Derksen.
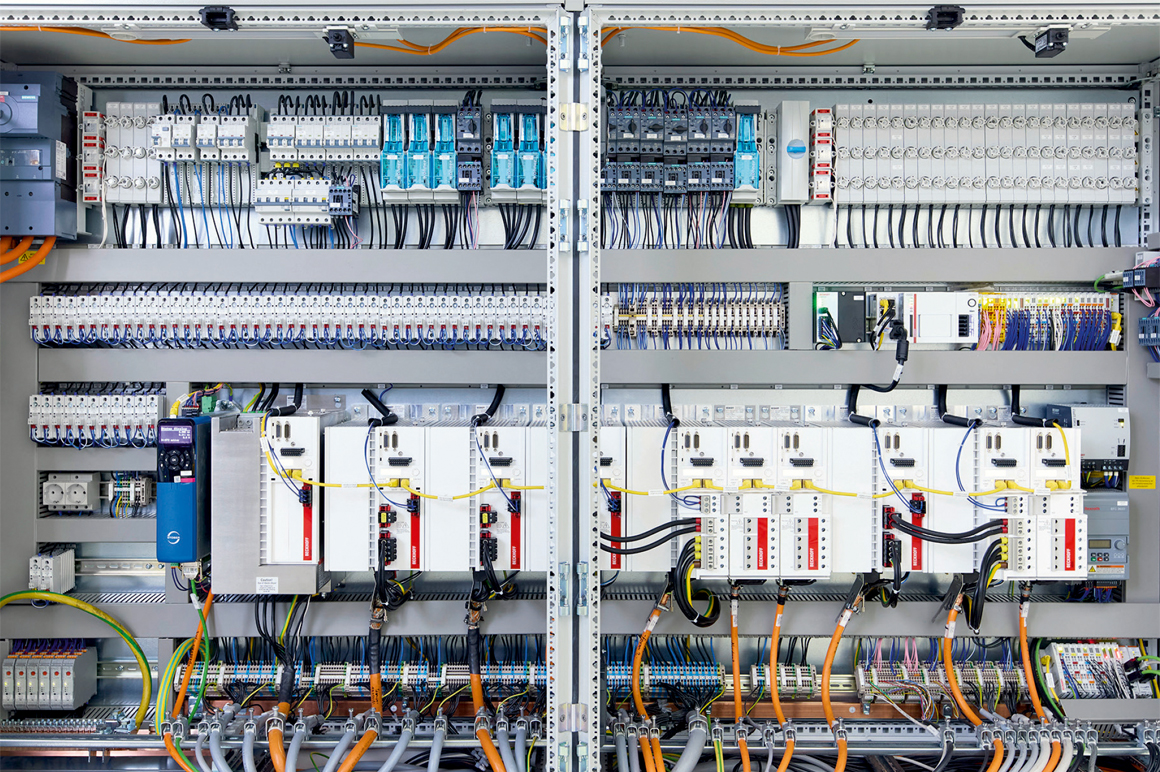
In addition to ease of operation, the issue of sustainability is becoming increasingly important in the plastics industry. BBM is doing its fair share of enabling customers to increase the proportion of recycled content in their products and reduce energy costs. According to BBM, switching from hydraulic systems to all-electric machines alone reduces energy consumption by around 50%. BBM can provide evidence of this using the energy data acquisition integrated in PC-based control with SCT2111 ring-type transformers and EL3443 EtherCAT Terminals for power measurement. An all-electric system from BBM consumes between 0.25 and 0.3 kW/kg of plastic. It is also possible to convert the energy consumption per unit, which is important information for calculating orders given today’s energy prices.
The roadmap is in place
Migrating the control architecture to other series is planned for the future. Felix Schulte comments: “With the hardware and software from Beckhoff, we’ve developed an excellent, high-performing overall package using which we can achieve our ideas in close cooperation with the Beckhoff experts.” Important topics for BBM include AI and algorithms that relieve operators of increasingly complex systems and control machines independently. The reasoning behind this is that blow molding – unlike injection molding – is an open process: opening the hall door or varying the batch material can have a noticeable effect on the process. “In future, our systems will be able to detect such influences and readjust the process independently.
Another aspect revolves around optimizing the system efficiency: The movement profiles of the drives can influence both energy consumption and cycle times. If an order urgently needs to be processed and finished, energy consumption is not the most important factor at this time. However, the system must apply the shortest possible cycle time.
So why not store several movement profiles (Eco, Standard, Speed) for the drive axes in the HMI and call them up as required to save time or energy? Predictive maintenance is another topic which BBM would like to manage to a greater extent using the control system in the future. The trend in motor current consumption is a good indicator when it comes to mechanical wear. Jerking in the movement profile is a clear indicator of worn bearings. All these measures help BBM’s customers to produce items in a more sustainable manner: A well-maintained system produces more efficiently. With PC-based control, such functions can be easily integrated and implemented in the existing control architecture.