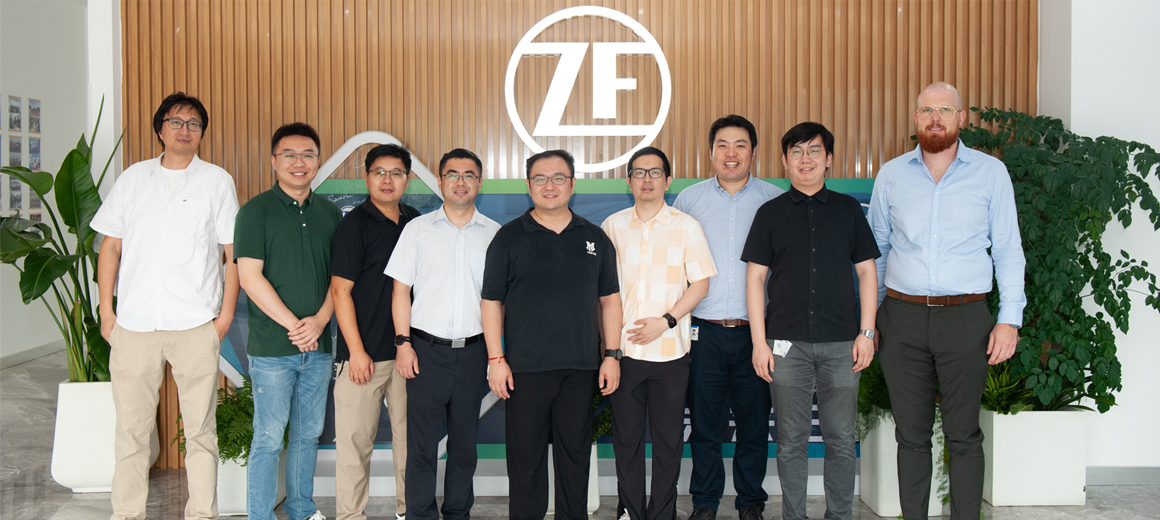
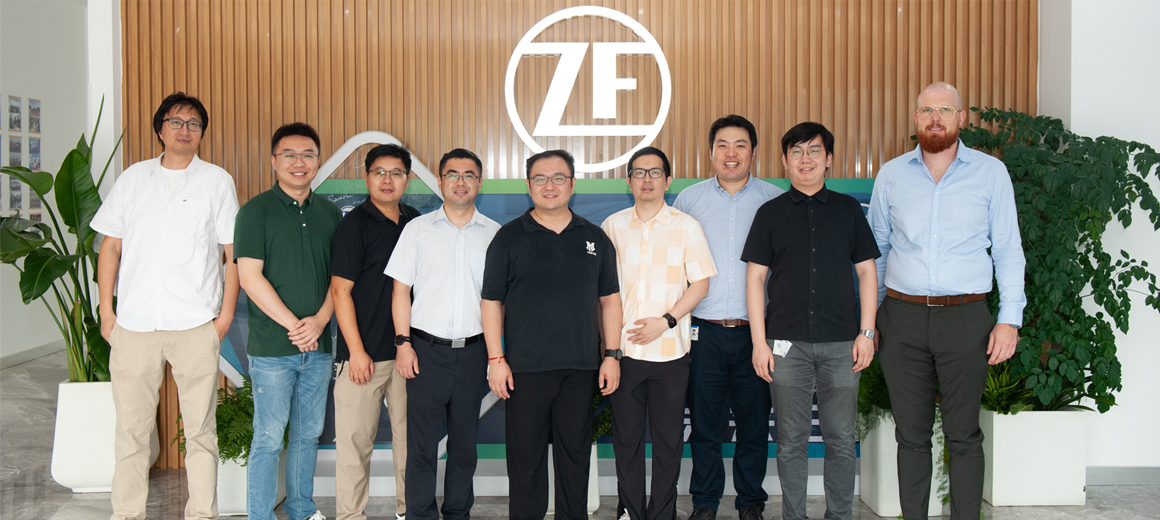
PC-based control and EtherCAT for a new era of chassis-by-wire technology
As a global leader in automotive components, ZF is at the forefront of the mobility transformation with its innovative and sustainable technologies. A pioneer in chassis-by-wire systems, ZF also requires advanced manufacturing technology for its brake-by-wire products to achieve faster, more efficient production with higher quality. The production line in China comprises numerous assembly lines with sophisticated core processes. A comprehensive range of Beckhoff components and solutions were used to overcome the associated challenges.
The Beckhoff automation solution for the new production line uses the high-performance C6675 control cabinet Industrial PC with TwinCAT software, along with EtherCAT I/Os featuring XFC technology, AX5000 and AX8000 series servo drives, and the XTS intelligent transport system. Bu Yuli, responsible for Advanced Manufacturing Engineering in the solenoid valve cartridge division at ZF in China, confirms the efficiency of this seamless, PC-based control technology: “The first thing we noticed after implementing the Beckhoff solution was a remarkable reduction in the production cycle time for solenoid valve cartridges, from 2.6 to just 2.4 seconds per unit. This improvement represents a significant increase in productivity that was achieved simply by switching to a Beckhoff controller and EtherCAT.”
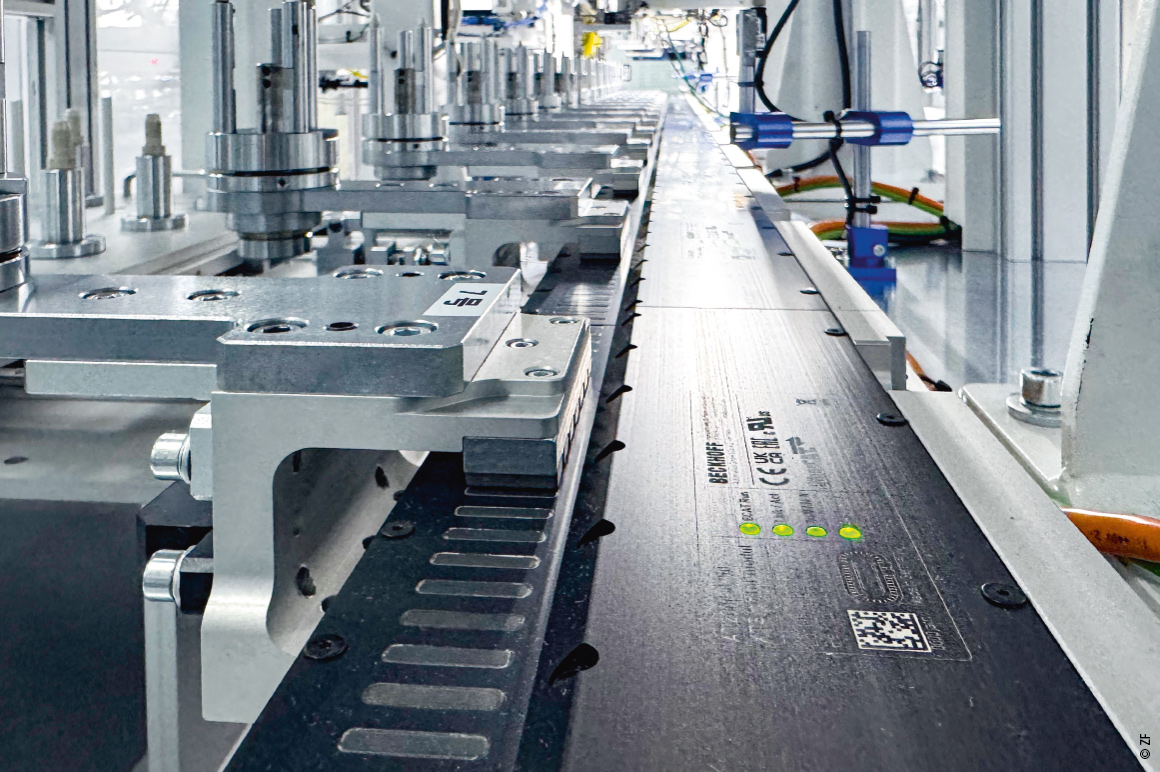
PC-based control technology from Beckhoff is industrial-grade, utilizing standard PC hardware such as multi-core processors and, in this instance, the high-performance x86 architecture to deliver exceptional computing power. This enables the system to manage sophisticated control tasks and large data sets while meeting the high performance requirements of advanced industrial automation. In combination with EtherCAT’s ultra-fast real-time response and high-speed data transmission, previous delays caused by signal interactions are also significantly minimized. What’s more, the oversampling technology and the TwinCAT 3 Scope software oscilloscope would help to quickly identify potential optimizations and effectively shorten bottleneck processes during programming.
Platform integration and cost savings
“The PC-based control platform not only enables the seamless integration of Manufacturing Execution Systems (MES) and IoT applications, but also works seamlessly with the ZF testing systems. This platform-based solution simplifies system setup and maintenance, delivers significant cost savings, and improves overall operational efficiency,” explains Shi Wenjie, responsible for testing in ZF’s Advanced Manufacturing Engineering division.
ZF chose the C6675 control cabinet Industrial PC for this production line due to its standardized and modular hardware design, which allows for flexible and demand-oriented configuration and upgrades. The high performance also meant that previously separate software systems for data acquisition, analysis, and motion control could be integrated into the C6675, thereby reducing overall costs. Beyond that, tasks that previously required other control platforms are enabled through TwinCAT Interface for LabVIEW™ or the Beckhoff I/Os and servo drives. Going forward, AI-based quality tools will also be integrated via TwinCAT 3 Machine Learning to increase productivity further still.
Efficient multi-user commissioning
With an increasing number of machine and device functions being implemented via software, it is now standard for multiple programming teams to work on the control code and commissioning. This can lead to challenges during the commissioning process, such as limited access to the version control system, discrepancies between the current status of the software on the machine and the local system, and errors resulting from irreversible changes. “Our extensive production line often requires integration and commissioning by multiple engineers, which has led to collaboration issues in the past,” adds Tian Xiaofei, responsible for Advanced Manufacturing Engineering in production line development.
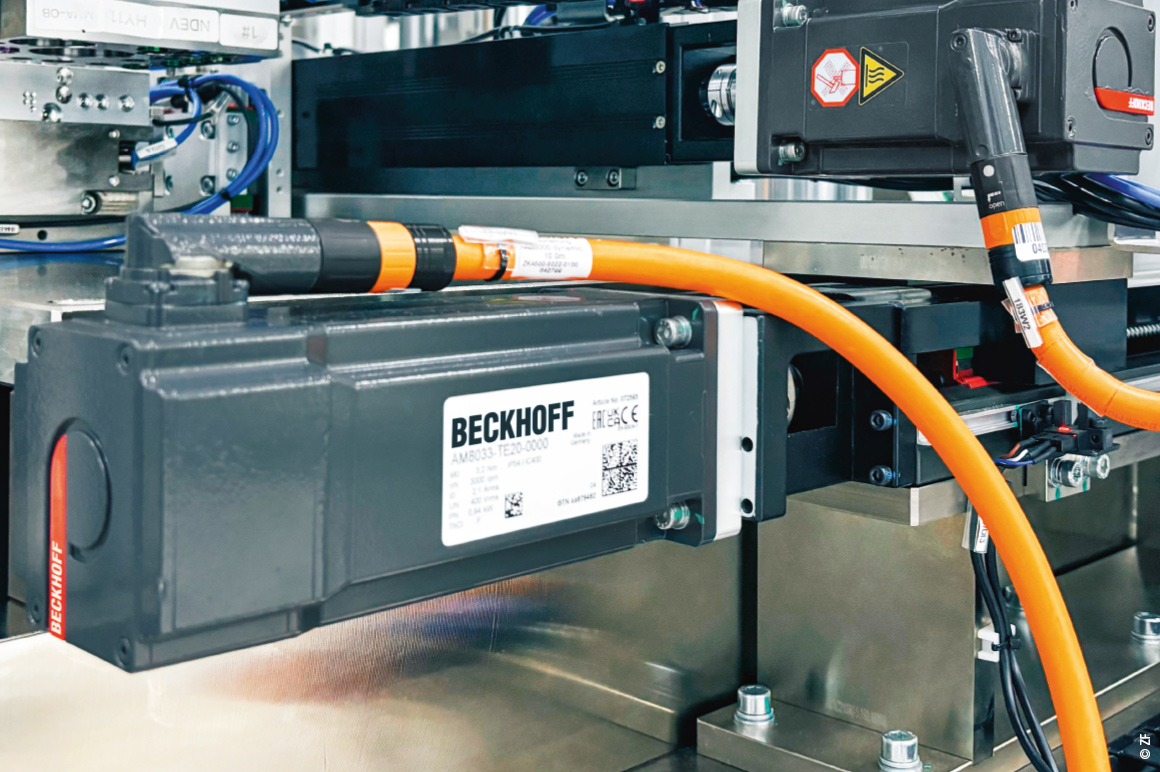
TwinCAT’s multi-user commissioning function now allows multiple engineers to work on the same project at the same time, without requiring specific knowledge of version control. Version control is built into the standard workflow and automatically transfers the current project status to the target system, while creating a history of all changes – including user names, timestamps, and comments on each change. “With the multi-user function, we have achieved both efficiency and time savings during commissioning. The history function also helps us to track changes throughout the program,” confirms Tian Xiaofei.
Flexible and efficient installation with XTS
“We have implemented Beckhoff’s XTS intelligent transport system on several production lines to assemble critical parts while ensuring flexibility and efficiency,” says Shi Anton, Advanced Manufacturing Manager at ZF. “The XTS movers, which are independently, precisely and quickly positionable, allow us to achieve high-quality assembly of parts. What’s more, the individually controllable movers allow for dynamic configurations of the production lines. By loading different recipes, the movers can remain in predetermined positions to enable one-touch product transfer in the production line. In addition, the special topology support of the XTS facilitates a compact line design and maximizes space on the production floor.”
In the assembly process, where a small percentage of products may be defective, real-time inspection is crucial to ensure the reliability of brake control systems. XTS improves inspection efficiency by enabling fast and precise control of the mover position and speed. The flexible mover movements allow defective products to be diverted to an analysis station for manual inspection – a benefit that is difficult to achieve with conventional transport systems. “The use of XTS in our assembly line has made production considerably more flexible. The motion control allows us to achieve faster cycle times, while the programmable flexibility ensures smooth transitions between different positions. The generous loading space and versatile layout of XTS also allows us to test more sophisticated production processes without having to remove products from their pallets,” explains Li Xiao, Advanced Manufacturing Manager at ZF. “We also see further potential for the future in using the XPlanar planar motor system to improve existing assembly and manufacturing processes. That said, we still need more time to validate it for specific applications.”
Conclusions
Beckhoff’s PC-based control system, particularly XTS, has demonstrated exceptional performance and adaptability in chassis-by-wire production lines, according to ZF. With faster cycle times, efficient platform integration, multi-user commissioning, and advanced control functions, ZF has been able to achieve significant improvements in both productivity and product quality. “ZF is committed to continuous innovation to increase the competitiveness and adaptability of future production lines by integrating new technologies such as XPlanar, TwinCAT Vision, MX-System, and XFC,” summarizes Li Xiao.